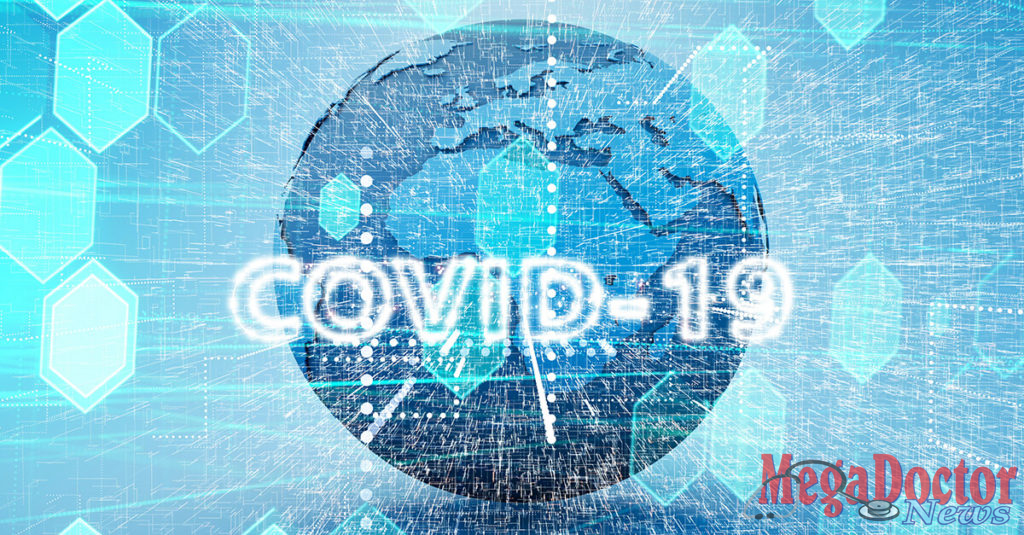
Mega Doctor News
PORTLAND, Ore. — Organizations can learn how to create safer, healthier workplaces with a free webinar that will teach new systems thinking to combat COVID-19 based on manufacturing principles designed to improve efficiency. The visible, comprehensive changes Clean Practice recommends also reduce fear and improve employee morale during a stressful time.
Indow, a clean-tech manufacturing business, has adapted Lean principles to prevent the spread of COVID-19 coronavirus among its employees by eliminating transmission vectors. The system it developed—which the company’s founder has dubbed “Clean,” after “Lean” manufacturing—provides a template for organizations across the country looking to rapidly and effectively reduce the risk of illness transmission to employees and customers.
This April 10 free webinar will walk participants through the basics of implementingClean Practice including how to:
- Create an organization’s COVID-19 response plan
- Lead plan implementation
- Lead a Clean Gemba Walk
- Identify and implement Engineered Solutions
The webinar will review the fundamental concepts and tools used in Clean Practice, including plan creation, Visual Factory, Gemba Walks, Engineered Solutions, and Kaizen. Instructors will explain how to quickly implement these tools for immediate impact.
In early March, with the largest U.S. outbreak of COVID-19 in Seattle just 170 miles north of the company’s facility, Indow CEO Sam Pardue’s concern about employee safety and the wider community inspired him to develop Clean Practice.
The principles of Lean eliminate waste, quality problems, and inefficiencies in manufacturing and other business systems. Clean uses similar methodologies to reduce or eliminate disease transmission vectors in the workplace. The benefits are analogous to social distancing —reduced opportunities for the virus to spread. The goal at Indow is universal workforce participation and zero COVID-19 transmissions.
Drawing from the Lean practice of ‘Visual Factory,’ the team divided the 20,000 square foot facility into zones and placed brightly colored stickers at high hand traffic ‘touchpoints’ like light switches and doorknobs. Zone captains created a cleaning schedule with every person in the organization covering one shift in each zone. The result: a system that effectively cleans all high-touch areas on a regular basis, with responsibility for work distributed across the staff.
Since Clean incorporates continuous improvement, the Indow team is already refining elements by moving beyond cleaning to eliminate disease vectors altogether. Among many changes, Indow removed doorknobs and added hooks to allow doors to be opened with forearms rather than fingers, eliminating high-touch potential illness transmission points.
For more information on the Indow Clean Manufacturing illness prevention system, visit www.cleanpractice.org
Clean Practice is meant to complement aggressive social distancing and is not a substitute. Indow endorses an immediate, nationwide, month-long shutdown. Everyone can use the time away to develop Clean Practices and return to much safer workspaces.
Core Principles of Clean Manufacturing
- Create a plan.
- Build trust through open communication and by sharing your plan.
- Full buy-in. Everyone from the CEO to new hires participates.
- Use Gemba Walks to inspect your facility for potential COVID-19 transmission vectors.
- Implement Visual Factory by using easy-to-follow visual indicators and guides to reduce training time and reinforce proper practices.
- PDCA Plan (establish a plan and expected results), Do (implement plan), Check (verify expected results achieved), Act (review and assess; do it again).
- Use Kaizen (continuous improvement) to improve upon first efforts.
a. Innovate and collaborate.
- Expand trust by extending protection to all your workers through a generous sick leave policy. This is critical to avoid a dangerous disease vector: sick employees coming to work because their families cannot survive without their wages.
- Accountability.
- Grow.